In the rapidly evolving landscape of industrial automation and electric motor development, precision and reliability are non-negotiable. Companies seeking to optimize motor performance, validate engineering designs, or ensure regulatory compliance require test equipment that delivers unmatched accuracy while withstanding demanding operational conditions. This is where hysteresis-based technologies and advanced motor dynamometer systems emerge as game-changers, combining cutting-edge physics principles with smart digital integration.
THE SCIENCE BEHIND HYSTERESIS DRIVE SYSTEMS
At the core of these innovations lies the fascinating phenomenon of magnetic hysteresis – the lag between the magnetization of ferromagnetic materials and the applied magnetic field. Unlike traditional friction-based systems, hysteresis devices harness this natural magnetic resistance to create controllable braking and torque transmission mechanisms.
Hysteresis brakes utilize precisely engineered rotor discs containing magnetic materials that interact with controlled electromagnetic fields. When current flows through the brake's stator coils, it generates a magnetic circuit that induces eddy currents in the rotor. The resulting resistance creates smooth, wear-free torque that can be adjusted in real-time with exceptional linearity. This makes them ideal for applications requiring precise tension control in web handling systems or delicate torque regulation in medical device testing.
Hysteresis dynamometers take this principle further by integrating torque measurement capabilities directly into the energy absorption process. Their non-contact operation eliminates mechanical wear components while maintaining consistent performance across millions of test cycles. Automated motor testing for household devices for testing actuator motors in satellite deployment mechanisms, where traditional friction-based systems would introduce particulate contamination risks.
In power transmission applications, hysteresis clutches stand out for their ability to deliver slip-controlled torque without physical contact between components. By adjusting the coil current, operators can create infinitely variable slip conditions – a critical feature for simulating real-world load scenarios during electric vehicle transmission testing or prototyping industrial servo systems.
ADVANCEMENTS IN MOTOR TEST SYSTEM ARCHITECTURE
Modern motor test systems have evolved into comprehensive validation platforms that combine hysteresis components with sophisticated measurement technologies and AI-driven analytics. A typical advanced motor test bench now integrates:
1. Multi-axis dynamometers capable of simulating complex load profiles
2. High-bandwidth power analyzers for efficiency mapping
3. Thermal imaging systems for hotspot detection
4. NVH (Noise Vibration Harshness) measurement arrays
5. Cloud-connected data management suites
Leading manufacturers now offer modular motor test equipment configurations that can scale from compact benchtop units for drone motor prototyping to megawatt-scale installations for wind turbine generator validation. The latest systems incorporate adaptive control algorithms that automatically adjust test parameters based on real-time performance data, significantly reducing setup times for complex duty cycle simulations.
BREAKTHROUGH APPLICATIONS ACROSS INDUSTRIES
The versatility of hysteresis-based systems is driving innovation across multiple sectors:
Electric Vehicle Development
Automotive engineers leverage hysteresis dynamometers to simulate road load conditions with unprecedented accuracy. By replicating exact gradient profiles and regenerative braking scenarios, test systems can optimize battery range predictions and thermal management strategies. Integrated Motor diagnostics tools perform combined validation of traction motors, power electronics, and battery systems in synchronized test sequences.
Industrial Robotics
As collaborative robots become more sophisticated, hysteresis clutches enable safe torque limiting in robotic joints. Motor test equipment specifically designed for robotic actuators evaluates both dynamic response and failure modes, ensuring compliance with stringent functional safety standards.
Renewable Energy Systems
Wind turbine manufacturers employ large-scale hysteresis brakes in their nacelle test rigs to simulate years of operational stress within compressed test cycles. Specialized motor dynamometer systems validate the performance of pitch control motors under extreme temperature and vibration conditions.
Aerospace and Defense
The non-magnetic nature of certain hysteresis brake configurations makes them invaluable for testing spacecraft components that must avoid ferromagnetic interference. Custom motor test systems for drone propulsion units combine altitude simulation chambers with torque response analyzers to validate performance under low-pressure conditions.
EMERGING TRENDS IN TEST METHODOLOGY
As global industries push toward higher efficiency standards, motor test systems are evolving beyond traditional performance validation:
Energy Recirculation Technology
Modern dynamometer systems incorporate regenerative power electronics that can feed up to 90% of absorbed energy back into the grid during testing. When combined with hysteresis-based loading, this creates ultra-efficient test environments for high-power motors.
Digital Twin Integration
Advanced systems now interface with CAD and simulation software to compare physical test results with digital twin predictions in real time. This closed-loop validation process accelerates design iterations while improving model accuracy.
Edge Computing Capabilities
Embedded processing units in next-gen motor test equipment perform localized data analysis, enabling immediate parameter adjustments without cloud latency. This proves critical when testing safety-critical systems like autonomous vehicle steering motors.
Material Science Innovations
Recent breakthroughs in amorphous magnetic materials have pushed hysteresis device capabilities to new levels. Some cutting-edge brakes now achieve torque density improvements of 40% compared to conventional designs while maintaining zero mechanical wear characteristics.
CHALLENGES AND SOLUTIONS IN MODERN MOTOR TESTING
While hysteresis-based systems address many traditional testing limitations, modern engineers face new challenges that require innovative approaches:
High-Speed Testing Demands
As brushless DC motors achieve rotational speeds exceeding 100,000 RPM, traditional contact-based measurement systems become impractical. The latest non-contact hysteresis dynamometers solve this with fiber-optic torque sensors and air-bearing supported rotors that eliminate mechanical drag.
Ultra-Low Torque Measurement
Medical device manufacturers testing micro motors for surgical robots require nano-scale torque resolution. Advanced systems now combine hysteresis load units with laser-based measurement technologies capable of detecting torque variations smaller than 0.001 Nm.
EMC Compliance Testing
Integrated test solutions now package hysteresis components with RF-shielded enclosures and precision power quality analyzers to simultaneously validate motor performance and electromagnetic compatibility during development.
THE HUMAN FACTOR IN TEST SYSTEM DESIGN
Beyond technical specifications, successful motor test solutions require intuitive human-machine interfaces. Modern systems feature:
- Augmented reality overlays for test parameter visualization
- Voice-controlled test sequence activation
- Predictive maintenance interfaces that monitor component wear
- Multi-user access controls with audit trail capabilities
Ergonomic design principles have become paramount, with modular test bays allowing rapid reconfiguration between different motor types. Safety systems incorporating machine vision cameras can now detect abnormal vibrations or thermal patterns, automatically initiating shutdown protocols before hazardous conditions develop.
FUTURE HORIZONS
As industries worldwide accelerate their electrification efforts, the demand for advanced motor test solutions continues to grow. Emerging developments include:
Quantum Magnetic Sensing
Laboratory prototypes are demonstrating quantum-based magnetic field sensors that could increase torque measurement resolution by orders of magnitude.
Self-Learning Test Algorithms
Neural network-equipped systems that automatically optimize test parameters based on historical data patterns and real-time performance feedback.
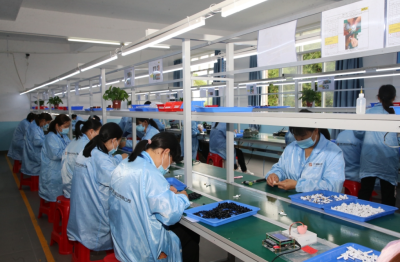
Locked-rotor testing systems that modify magnetic hysteresis properties in response to environmental conditions, enabling smart self-adjusting brake systems.
The integration of hysteresis technology with modern digital systems creates unprecedented opportunities for motor performance optimization. From micro-motors powering next-generation medical implants to gigawatt-scale generators enabling the renewable energy transition, advanced test equipment forms the backbone of technological progress.
Organizations that adopt these sophisticated testing solutions position themselves at the forefront of their industries, equipped to meet evolving challenges while accelerating innovation cycles. As motor systems grow increasingly complex and interconnected, the marriage of hysteresis principles with smart measurement technologies will continue to redefine what's possible in electromechanical engineering and quality assurance.
This technological synergy doesn't just improve product development – it enables the creation of motors that are more efficient, reliable, and intelligent than ever before. Whether optimizing an existing design or pioneering breakthrough technologies, modern hysteresis-based test systems provide the precision toolkit needed to turn engineering visions into operational realities.