In dc motor test -evolving landscape of industrial automation and electric motor development, the demand for accurate testing solutions has never been greater. From automotive manufacturers pushing the boundaries of electric vehicle performance to aerospace engineers demanding unprecedented reliability, the tools we use to validate motor performance are becoming as crucial as the motors themselves. At the heart of this technological revolution lie several critical components: hysteresis brakes, hysteresis dynamometers, hysteresis clutches, and their integration into comprehensive motor test systems.
The Science Behind Hysteresis Technology
Hysteresis-based devices leverage the unique magnetic properties of specialized materials to create controllable resistance forces. Unlike traditional friction-based systems that wear down over time, hysteresis devices maintain consistent performance through electromagnetic principles. This fundamental characteristic makes them indispensable for applications requiring precise torque control and repeatable measurements.
When Wire winding through the excitation coil of a hysteresis brake, it creates a magnetic field that induces eddy currents in the rotor. The interaction between these currents and the magnetic field generates a smooth, wear-free braking torque that can be precisely controlled through current adjustments. This same principle applies to hysteresis clutches, where torque transmission occurs without physical contact between components.
Hysteresis Dynamometers – The Gold Standard for Motor Testing
Modern hysteresis dynamometers represent the pinnacle of motor testing technology. These sophisticated devices combine the precision of hysteresis braking with advanced measurement capabilities, enabling engineers to:
- Accurately measure torque across wide speed ranges
- Simulate real-world load conditions with dynamic response
- Conduct continuous testing without performance degradation
- Capture data for efficiency calculations and performance mapping
A key advantage of hysteresis dynamometers lies in their ability to handle sudden load changes without mechanical shock. This capability proves particularly valuable when testing electric motors for applications requiring rapid acceleration/deceleration cycles, such as robotic actuators or electric vehicle drivetrains.
Motor Test Systems – Beyond Basic Measurement
Contemporary motor test systems have evolved into complete performance analysis platforms. A comprehensive motor test system typically integrates:
1. Hysteresis-based loading devices
2. Precision power analyzers
3. Environmental simulation chambers
4. Advanced control software
5. Data acquisition and reporting modules
These systems now perform complex evaluations including:
- Efficiency mapping across operating ranges
- Thermal performance analysis
- Vibration and acoustic profiling
- Endurance testing under simulated real-world conditions
- Regenerative energy recovery measurements
The integration of hysteresis clutches in these systems allows for unique testing configurations. Engineers can now create complex drivetrain simulations that replicate actual operating environments – from wind turbine gearboxes to hybrid vehicle power distribution systems – all within controlled laboratory conditions.
Applications Across Industries
The versatility of hysteresis-based testing equipment finds applications in numerous sectors:
Automotive Development
Electric vehicle manufacturers rely on hysteresis dynamometers for:
- Traction motor validation
- Battery system efficiency testing
- Regenerative braking analysis
- Thermal management system development
Industrial Automation
Motor test systems ensure optimal performance for:
- Servo motors in manufacturing robots
- Pump and compressor motors
- Conveyor system drives
- Precision positioning equipment
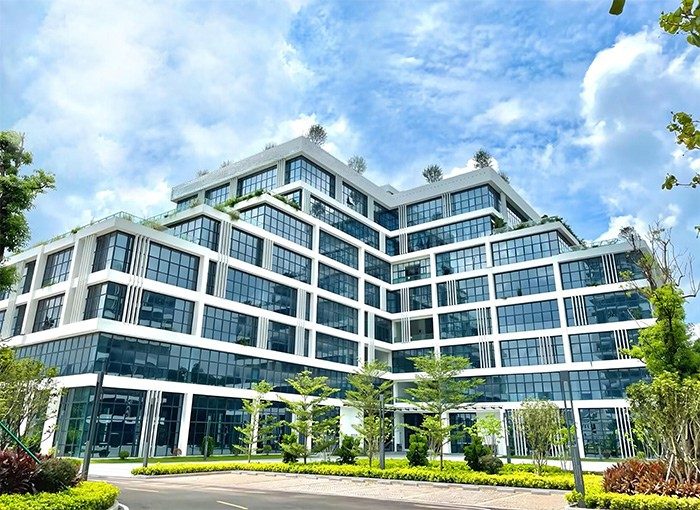
Aerospace and Defense
Specialized test systems address unique requirements:
- High-altitude performance simulation
- Extreme temperature operation testing
- Vibration resistance validation
- EMI compatibility testing
Renewable Energy
Hysteresis-based solutions contribute to:
- Wind turbine generator testing
- Solar tracking motor validation
- Hydroelectric system efficiency optimization
- Energy storage system integration testing
Technical Innovations Driving Progress
Recent advancements in hysteresis technology have significantly enhanced testing capabilities:

Adaptive Control Algorithms
Modern systems employ AI-driven control algorithms that:
- Automatically adjust test parameters
- Predict system behaviors
- Optimize test sequences
- Detect anomalies in real-time
Energy Recovery Systems
Next-generation dynamometers incorporate regenerative power systems that:
- Recapture up to 90% of test energy
- Reduce facility power consumption
- Enable true four-quadrant testing
- Lower operational costs
Multi-Axis Testing Capabilities
Advanced test stands now combine:
- Torque measurement
- Radial/axial load simulation
- Vibration analysis
- Thermal mapping
This holistic approach provides complete mechanical and electrical performance profiles in a single test cycle.
Choosing the Right Testing Solution
Selecting appropriate test equipment requires careful consideration of several factors:
Torque and Speed Ranges
Ensure the system covers both current requirements and future scalability. Look for devices offering:
- Wide speed ranges without torque drop-off
- Smooth torque control at low speeds
- High overload capacity
Measurement Accuracy
Critical parameters to evaluate:
- Torque measurement resolution
- Speed measurement accuracy
- Electrical parameter sampling rates
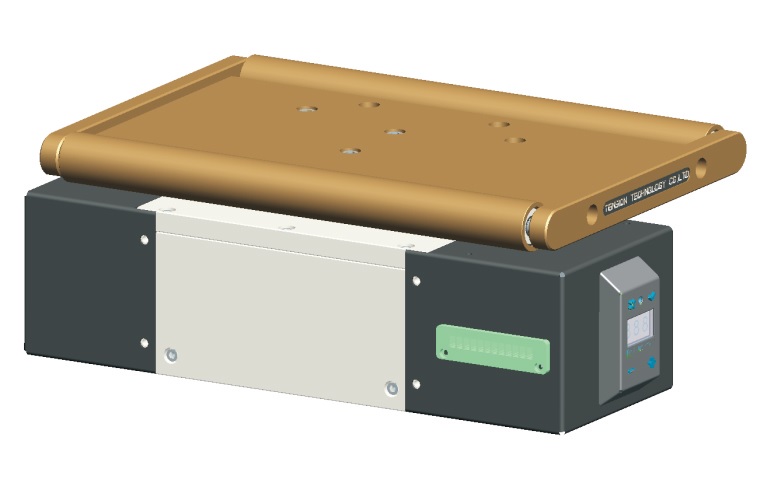
- Temperature measurement precision
System Integration
Consider compatibility with:
- Existing laboratory infrastructure
- Data management systems
- Third-party analysis software
- Future expansion capabilities
Regulatory Compliance
Verify compliance with relevant standards:
- ISO 17025 for calibration laboratories
- IEC standards for electrical safety
- Industry-specific certification requirements
The Future of Motor Testing
Emerging trends are shaping the next generation of testing solutions:
Digital Twin Integration
Combining physical testing with virtual simulations through:
- Real-time data exchange with digital models
- Predictive performance analysis
- Virtual prototype validation
IoT Connectivity
Smart test systems featuring:
- Remote monitoring capabilities
- Cloud-based data storage
- Automated reporting functions
- Predictive maintenance alerts
Sustainable Testing Practices
Development of:
- Zero-emission test facilities
- Closed-loop energy systems
- Recyclable component designs
- Low-power standby modes
Customizable Solutions
Growing demand for:
- Modular system architectures
- Application-specific test profiles
- Rapid reconfiguration capabilities
- Scalable power handling
Implementing Effective Testing Protocols
To maximize the value of hysteresis-based test systems, engineers should:
1. Develop tensioning system covering all operational scenarios
2. Implement rigorous calibration routines
3. Establish data management protocols
4. Train personnel on system capabilities and limitations
5. Regularly review and update testing procedures
Case Study – Revolutionizing EV Motor Development
A leading electric vehicle manufacturer recently implemented a hysteresis-based motor test system that reduced development time by 40%. The system's ability to perform continuous durability testing with precise load control enabled engineers to:
- Identify thermal management issues early
- Optimize motor efficiency across speed ranges
- Validate regenerative braking performance
- Accelerate certification processes
Maintenance and Longevity Considerations
Proper maintenance ensures optimal performance and extends equipment lifespan:
Regular Maintenance Tasks
- Magnetic particle inspection of hysteresis discs
- Cooling system checks
- Bearing lubrication
- Electrical connection verification
- Software updates
Calibration Best Practices
- Follow manufacturer-recommended intervals
- Use traceable calibration standards
- Maintain environmental controls
- Document all calibration activities
Troubleshooting Common Issues
Typical challenges and solutions:
- Torque fluctuations – Check excitation current stability
- Overheating – Verify cooling system operation
- Signal noise – Inspect grounding connections
- Software communication errors – Update drivers and firmware
The Economic Advantage
While hysteresis-based systems require initial investment, they offer significant long-term benefits:
- Reduced downtime through reliable operation
- Lower maintenance costs compared to friction systems
- Energy savings through regenerative capabilities
- Improved product quality through precise testing
- Compliance with evolving industry standards
Conclusion
As industries continue to push the boundaries of electromechanical performance, hysteresis-based testing solutions stand as essential tools in the pursuit of innovation. From the fundamental physics of magnetic hysteresis to the complex integration of modern motor test systems, these technologies enable engineers to verify, validate, and improve motor designs with unprecedented precision. Whether developing cutting-edge electric vehicles or refining industrial automation systems, the proper implementation of hysteresis brakes, dynamometers, and clutches within comprehensive test environments remains critical to achieving technical excellence and maintaining competitive advantage in today's fast-paced technological landscape.