In the world of industrial engineering and motor testing, precision is not just a buzzword—it’s the bedrock of innovation. From automotive research labs to aerospace manufacturing floors, the demand for accurate, repeatable, and efficient testing solutions has never been higher. Enter the unsung heroes of this domain: hysteresis brakes, hysteresis dynamometers, hysteresis clutches, and the sophisticated motor test systems that integrate them. These technologies are the silent workhorses behind the scenes, ensuring that motors, engines, and mechanical systems meet the rigorous standards of performance, safety, and durability. Let’s dive into how these tools are transforming industries and why they deserve a spotlight in your next testing setup.
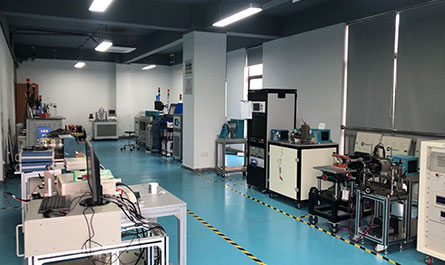
THE SCIENCE OF HYSTERESIS: A BRIEF OVERVIEW
Hysteresis, a term derived from the Greek word for “lagging behind,” refers to the phenomenon where the state of a system depends on its history. In practical terms, hysteresis devices leverage magnetic or mechanical lag to generate controlled resistance or torque. This principle is elegantly simple yet remarkably effective, making hysteresis-based equipment ideal for applications requiring smooth operation, minimal maintenance, and exceptional accuracy.
HYSTERESIS BRAKES: WHERE CONTROL MEETS DURABILITY
Hysteresis brakes are the epitome of low-maintenance torque control. Unlike magtrol dynamometer , which rely on physical contact and wear over time, hysteresis brakes operate contact-free. A rotating disc passes through a magnetic field, inducing eddy currents that create resistance. This resistance is proportional to the input current, allowing for precise torque modulation without mechanical degradation.
Applications abound. In conveyor systems, hysteresis brakes ensure consistent tension control, preventing product damage during high-speed operations. In fitness equipment, they enable adjustable resistance levels for smooth, silent workouts. For electric vehicle manufacturers, hysteresis brakes are indispensable in dynamometer testing, simulating real-world driving conditions to validate motor efficiency and battery performance.
The advantages are clear: zero wear, minimal heat generation, and unparalleled controllability. By eliminating friction, hysteresis brakes reduce downtime and operational costs, making them a long-term investment for industries prioritizing reliability.
HYSTERESIS DYNAMOMETERS: THE GOLD STANDARD IN MOTOR TESTING
When it comes to evaluating motor performance, hysteresis dynamometers are the go-to solution for engineers who refuse to compromise. These devices use the same hysteresis principle to absorb and measure torque, speed, and power output with microscopic precision. Whether testing a tiny servo motor for robotics or a massive industrial engine, hysteresis dynamometers deliver data that engineers can trust.
What sets them apart? For starters, their non-contact design eliminates the risk of mechanical wear, ensuring consistent performance over thousands of test cycles. Second, their rapid response time allows for dynamic load simulations—critical for applications like hybrid vehicle regenerative braking or wind turbine pitch control. Lastly, hysteresis dynamometers excel in low-speed testing scenarios, where traditional water or eddy current dynamometers struggle to maintain accuracy.
Industries from aerospace to renewable energy rely on these dynamometers to validate prototypes, optimize designs, and comply with international standards. Imagine a helicopter rotor being tested for emergency landing scenarios or a tidal power generator undergoing endurance trials—hysteresis dynamometers provide the reliability needed to push boundaries safely.
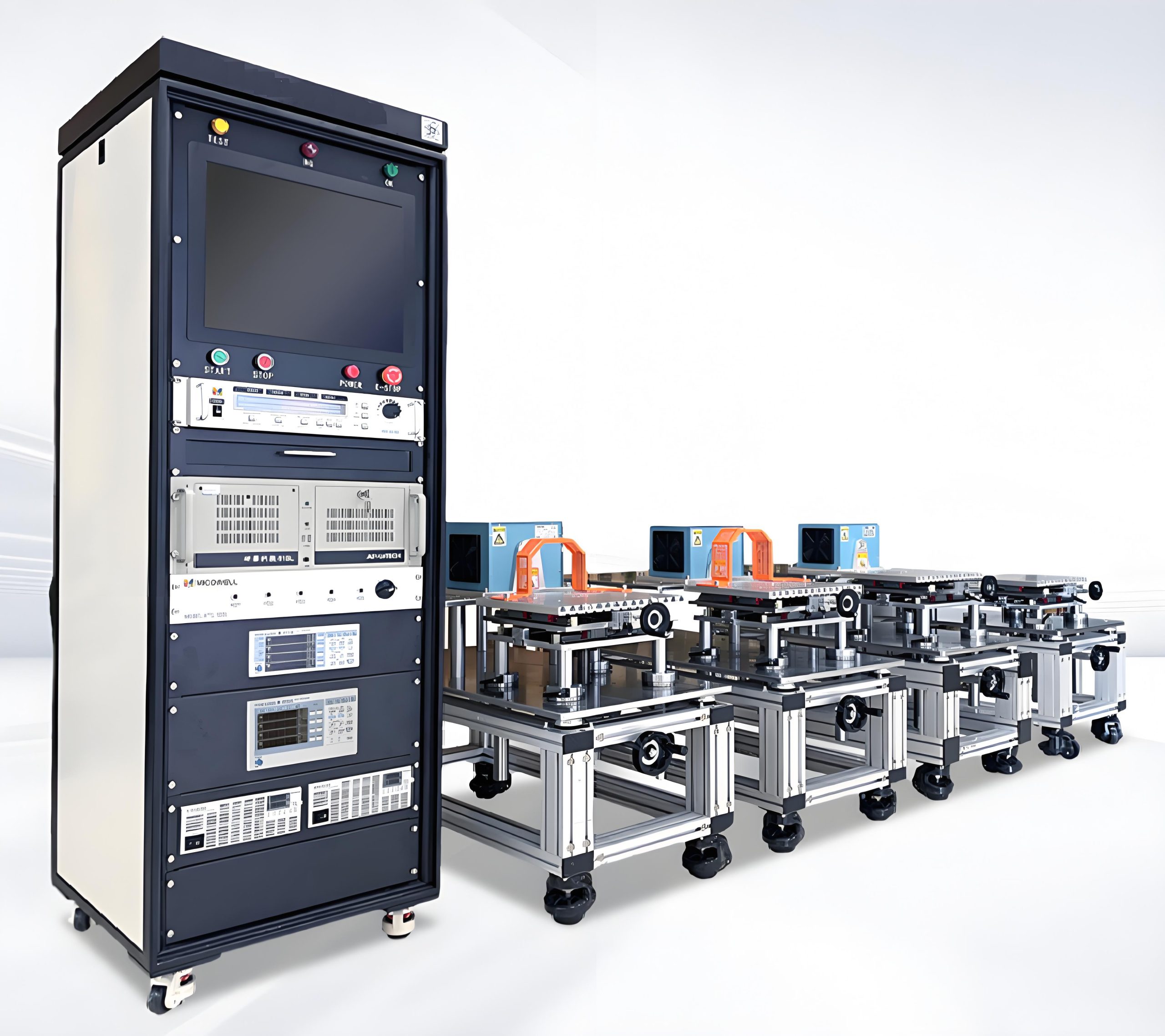
HYSTERESIS CLUTCHES: SMOOTH ENGAGEMENT, ZERO SLIP
While brakes and dynamometers hog the limelight, hysteresis clutches play a critical role in applications requiring precise torque transmission. These clutches use a magnetic field to engage two rotating components, offering slip-free power transfer and infinitely adjustable torque limits.
In packaging machinery, hysteresis clutches ensure delicate products like pharmaceuticals or electronics aren’t crushed during handling. In robotics, they enable safe human-machine collaboration by limiting joint forces. Even in renewable energy systems, these clutches protect wind turbine gearboxes from overloads during sudden gusts.
The absence of physical contact means no lubrication, no wear, and no downtime—a trifecta of efficiency for industries where uptime is revenue.
MOTOR TEST SYSTEMS: INTEGRATING THE FUTURE
Hysteresis devices shine brightest when integrated into comprehensive motor test systems. Modern motor test equipment goes beyond standalone tools, offering end-to-end solutions that combine hysteresis brakes, dynamometers, sensors, and advanced software. These systems automate data acquisition, perform real-time analytics, and generate actionable insights—all while simulating real-world conditions.
Take, for example, an electric vehicle motor test rig. A hysteresis dynamometer applies variable loads to mimic highway driving, uphill climbs, and regenerative braking. Simultaneously, thermal cameras monitor heat dissipation, while vibration sensors detect imbalances. The system’s software correlates this data, predicting motor lifespan and identifying potential failure modes before they occur.
For manufacturers, this integration slashes development cycles and reduces costly recalls. For R\u0026D teams, it unlocks new possibilities in material science and energy efficiency.
WHY CHOOSE HYSTERESIS-BASED SOLUTIONS?
The answer lies in three pillars: precision, reliability, and adaptability. Hysteresis technology eliminates the variables that plague mechanical systems—wear, lubrication, and temperature drift. It thrives in harsh environments, from sub-zero Arctic conditions to sweltering desert heat. And with the rise of IoT and Industry 4.0, these devices seamlessly integrate into smart factories, feeding data into predictive maintenance algorithms and digital twins.
CONCLUSION: POWERING TOMORROW’S INNOVATIONS
As industries evolve, so too must the tools that drive progress. Hysteresis brakes, dynamometers, clutches, and the motor test systems that harness them are not mere components—they are enablers of possibility. They empower engineers to test harder, design smarter, and innovate faster. Whether you’re developing the next generation of electric vehicles, refining industrial automation, or pushing the limits of renewable energy, these technologies offer the precision and reliability needed to turn vision into reality.
In a world where margins for error are shrinking, hysteresis-based solutions stand as guardians of quality. They don’t just meet standards—they redefine them.